Human Powered Vehicle racing (high school)
I was a member of the Kingswood College Human Powered Vehicle (HPV) racing team for three years from 2017 to 2019. We competed in three races each year, culminating in the Energy Breakthrough held in Maryborough. This contains a 24 hour endurance race where a team of eight riders complete as many laps as possible on a track with often over 100 vehicles on it.
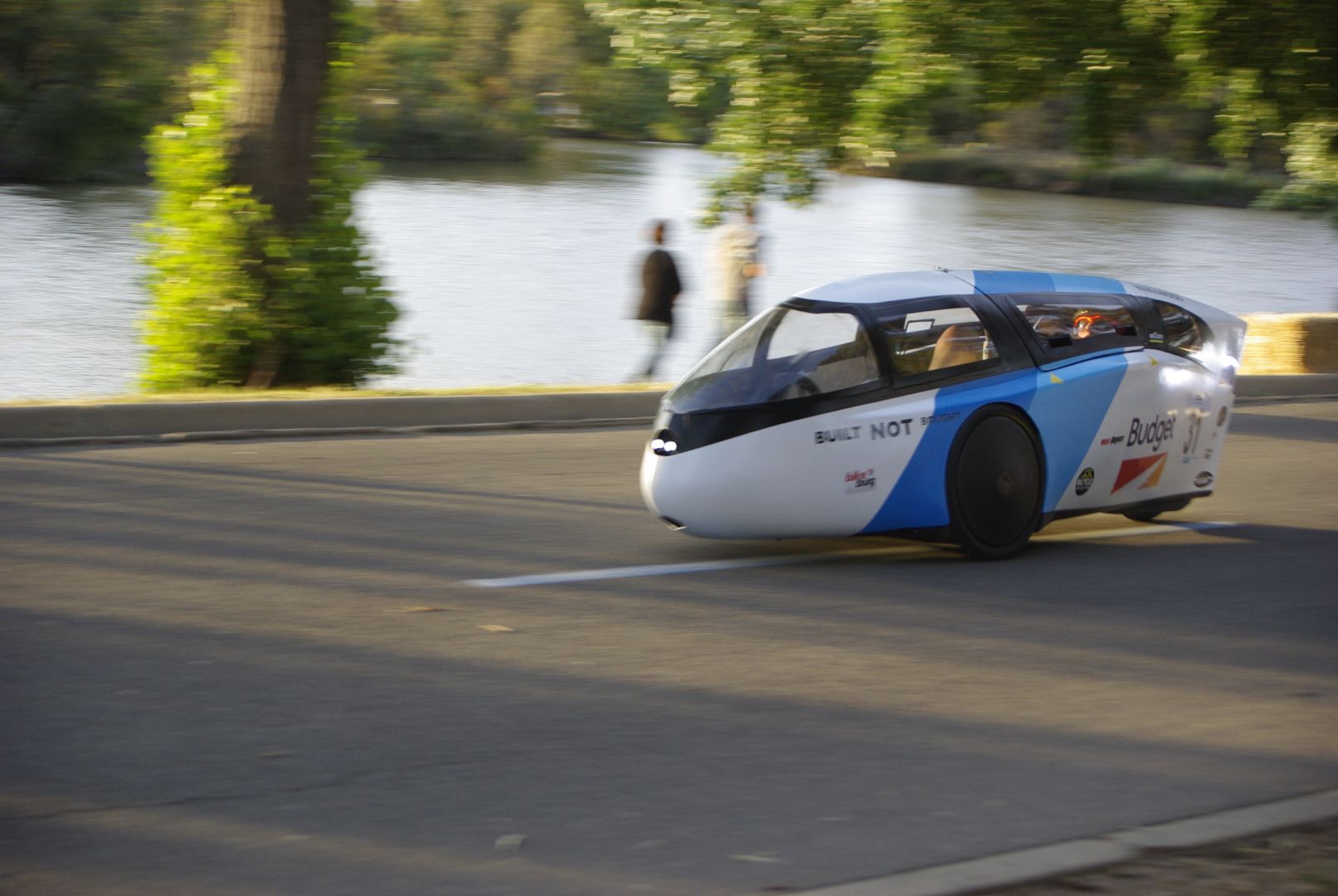
Jotham riding Evo during the 2019 Maryborough Energy Breakthrough qualifying session.
Throughout my time in the team, we built, heavily modified and significantly redesigned our vehicle “Evo” to obtain the best possible performance. I was heavily involved in the workshop side of the team and was a member of the pit crew in 2017. In 2018 and 2019 I was a rider as well as working on the mechanical and electrical aspects of the vehicle alongside the rest of my team.
The team has a youtube channel where highlights videos of races are shared.
Machining a smaller idler sprocket
Some of our modifications in 2019 required a smaller chain idler puller than what was easily available commercially at the time. Commercial idler sprockets were usually 15 teeth in size, however we needed one that was 11 teeth in size. I spent a significant amount of time designing and machining two sprockets to meet this requirement.
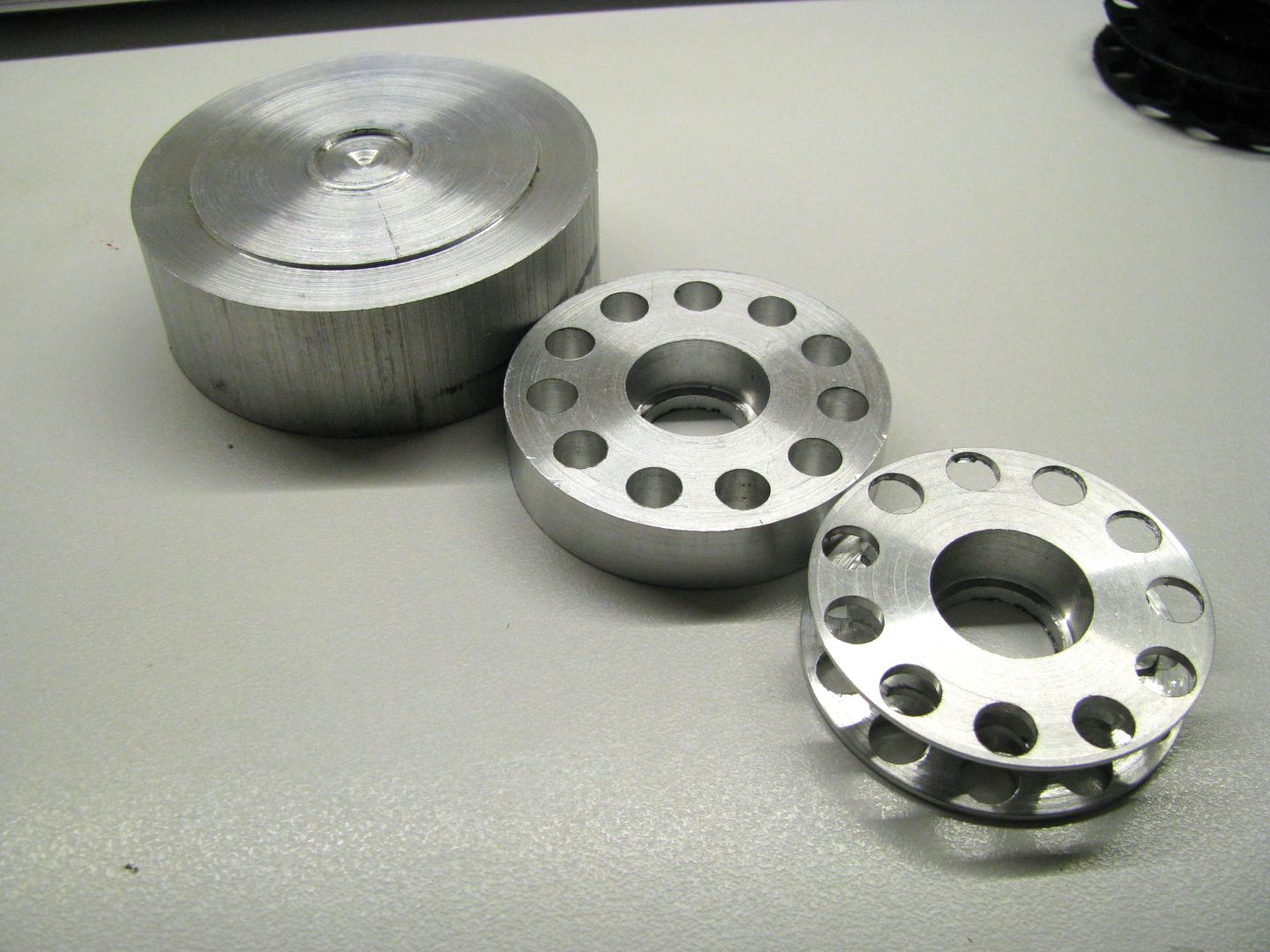
A finished idler sprocket next to a partially completed one and the stock material they were made from.
The sprockets were designed parametrically using FreeCAD. Blanks were cut on a band saw and turned to the rough size on a lathe. Inspiration was taken from a commercial design that did not require CNC machining or special tooling to form the teeth. The teeth were formed by drilling holes at a calculated radius using a rotary table in a milling machine before removing excess material using the lathe. The teeth are not full height and thus cannot transmit much torque, however this is not an issue for an idler sprocket.
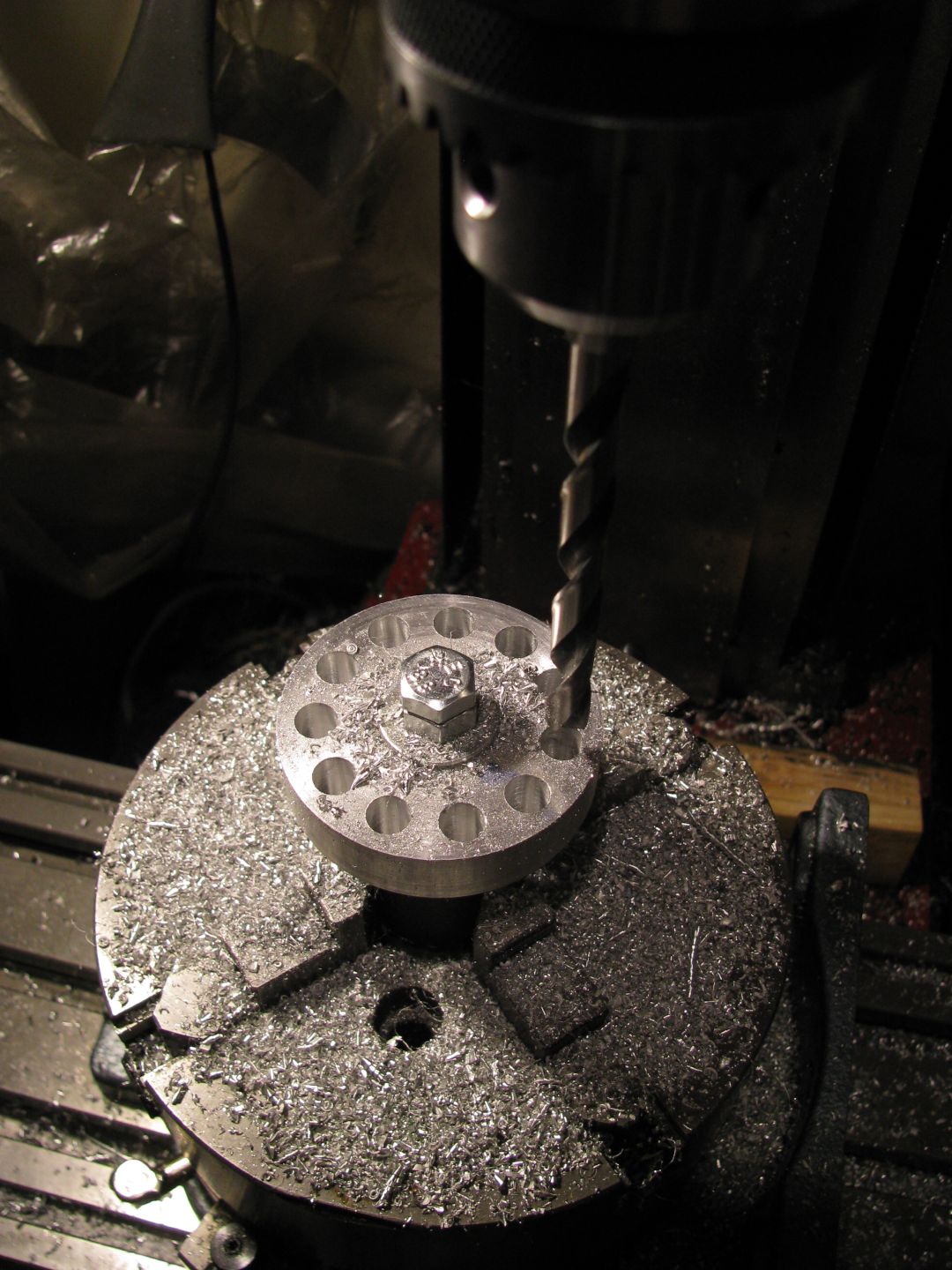
Drilling out the holes that form the base of the teeth.
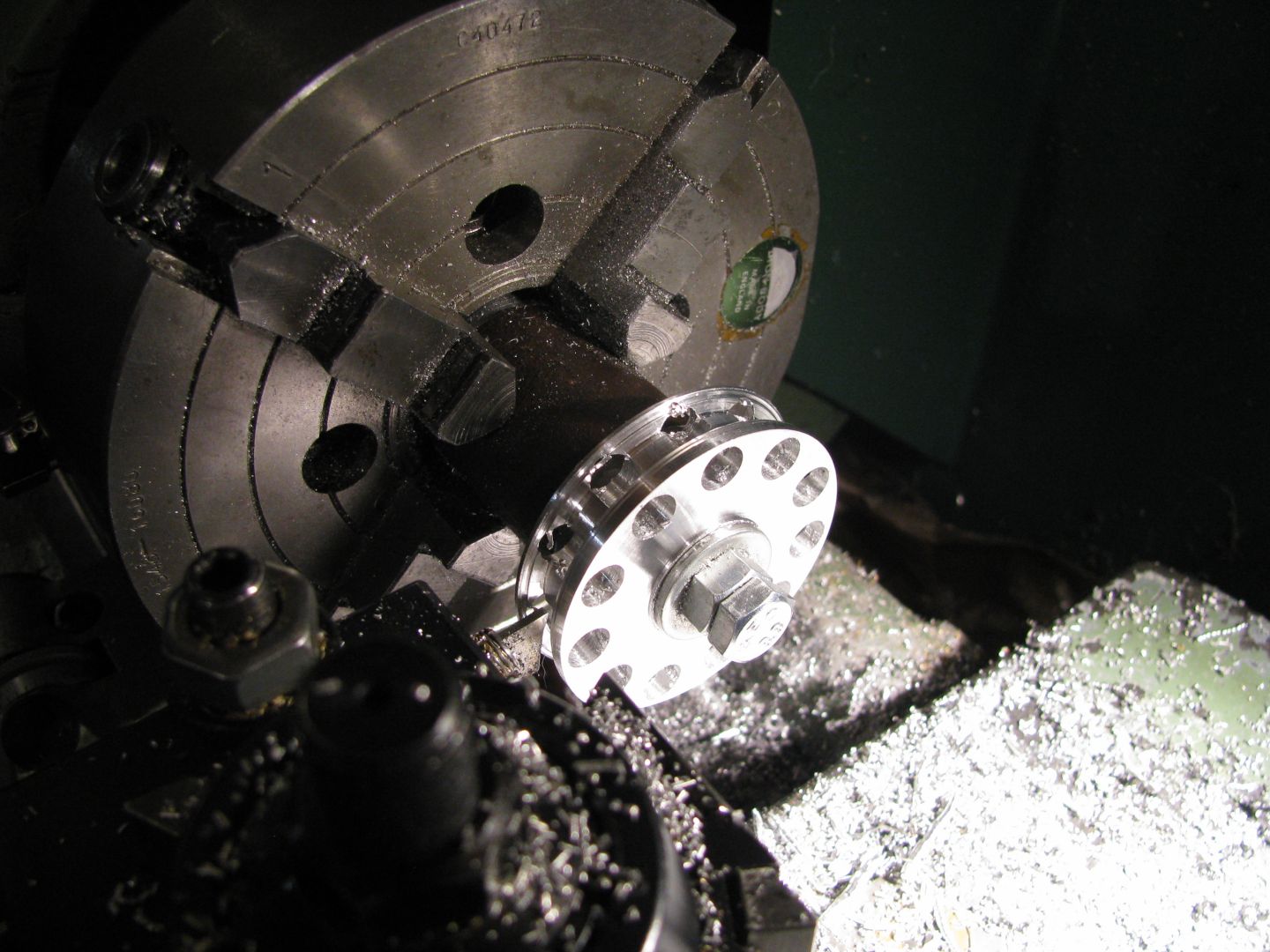
Turning down the outside of the sprocket to reveal the teeth.